Claas Group: Calculating tens of thousands of items with ORBIS PCC completely integrated in SAP ERP
Sectors: Mechanical and plant engineering
Processes: Finance & Controlling
References: CLAAS Gruppe
By moving to ORBIS Product Cost Calculator (ORBIS PCC), the CLAAS Group performs development accompanying calculations completely in SAP ERP – standardized, transparent and in high quality. Because the SAP-based add-on accesses the latest data and prices in SAP, the calculation is streamlined at the same time. The teamwork between costing, purchasing and work preparation also benefits as all data entered in the add-on immediately flow into SAP ERP and are immediately available.
CLAAS is the global leading manufacturer of agricultural machines. The company headquartered in the Westphalian Harsewinkel is the European market leader for combined harvesters. CLAAS is the world leader in its second largest product group, the self-propelled field choppers. The CLAAS product range also includes tractors, round and square ballers, forage harvesters, telescopic handlers and the EASY products in which CLAAS bundles its electronics expertise. CLAAS produces at four German and eight international sites and achieved a turnover of Euro 3.6 billion in 2016 with 11,300 employees worldwide.
Head office: Harsewinkel
Products: Agricultural machines
Production sites: 12 worldwide
Employees: 11,300 employees worldwide
Website: www.claas.de
Combine harvesters with more than 50,000 individual parts
To cement its position in the market, the CLAAS Group has always opted for high product quality as well and innovations.
“Our machines should help customers in optimizing their agricultural processes and achieving higher harvest yields”, says Uwe Oltmanns, System Analyst & Controller Corporate Purchasing, CLAAS KGaA mbH.
Our investments in R & D projects are correspondingly high: In 2012, the CLAAS group spent more than Euro 200 million on this.
For this reason if is even more important that the cost curve can be reliably calculated already in the early phase and that the manufacturer costs are aligned to the desired target costs as best as possible. However, the development accompanying calculation at CLAAS is unusually complex: One CLAAS LEXION 780 harvester for example, consists of almost 54,000 individual parts.
“Consequently, several tens of thousands of individual items need to be calculated for a new development, depending on product group and model”, explains Uwe Oltmanns.
In order to meet customers’ wishes, on average there are around 150 individual variants for each model – and each one has to be calculated separately.
SAP integrated calculation from A - Z
By changing to the ORBIS Product Cost Calculator (ORBIS PCC), an easy-to-work add-on which is fully integrated into the central SAP-ERP system, CLAAS creates the conditions for an efficient and transparent calculation, reliably and from one source. The introduction of the ORBIS solution, which replaces the calculation solution from another vendor, was performed within the framework of the “Purchasing Strategy 2020”, which focuses on greater cost transparency, more bundling effects and higher profitability.
“Following the integration of the calculation in SAP ERP, we now have a homogeneous database and a smooth flow of information between ORBIS PCC and ERP. The calculation is now performed IT-supported from A to Z, standardized, flexible and in great detail”, explains Jan Kirberich, Lead Engineer Simultaneous Product Costing of the CLAAS Group.
This significantly relieves the work load of the 15 end users at CLAAS – in the final stage this will increase to 30 –, who currently cost combine harvesters, field choppers, forage harvesters, square and round ballers and tractors with ORBIS PCC.
When a costing department employee enters the data and prices of the components for a new or further development into the add-on, this data flows directly into the SAP software, where it is immediately processes and booked correctly. The information is immediately available, also for follow-up processes in purchasing and in work preparation. This improves and speeds up the cross-departmental cooperation in the cost calculation process.
Online access to updated SAP data
Because the add-on can access current material and raw material prices, tariffs, overhead costs and exchange rates online via SAP ERP, the overall calculation can be performed much quicker than before. The time-consuming and error-prone manual reading of data and figures from SAP into a table calculation and the cumbersome back and forth copying, is eliminated. Also, the fact that individual assemblies of a combine harvester or field chopper can be calculated in various level of detail by number of carried-over parts per component, contributes to speeding up the calculations.
Source Photo: © CLAAS KGaA mbH
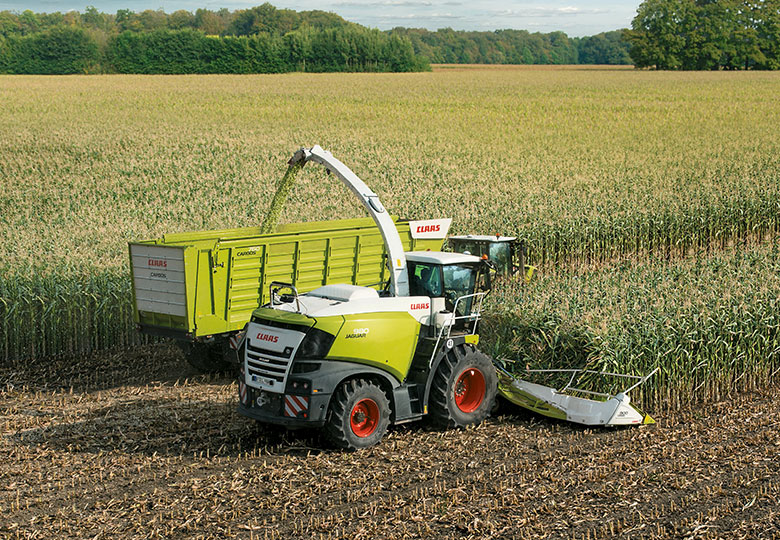
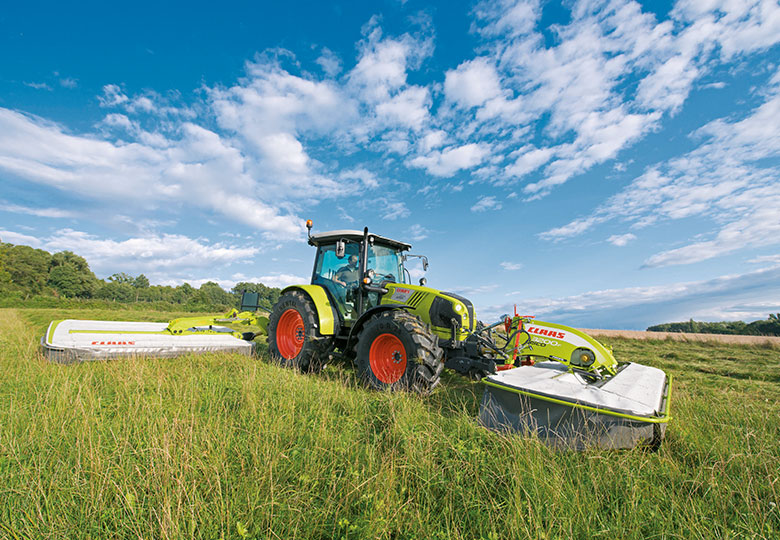
“Because some activities can now be done much easier and quicker, the product estimators have more time for their core tasks such as optimizing a costing with regard to quality and economic efficiency or identifying cost drivers”, explains Jan Kirberich.
In addition, price simulations with which manufacturing costs can be accurately predicted at an early time in ORBIS PCC, put Purchasing in a stronger position for negotiating with suppliers.
Source Photo: © CLAAS KGaA mbH
Updating calculations with the click of the mouse
As ORBIS PCC automatically works with the latest information from the SAP software, each calculation created in the add-on can be promptly adjusted and updated at any point in time. This is a critical business aspect, as in some cases the time frame from the creation of the construction concept to release for production can stretch over six years.
In order to keep the calculation updated, even when material and raw material prices, tariffs or foreign exchange rates change repeatedly in this time, CLAAS performs the relevant adjustments at the change of each business year. At this point in time, new prices or tariffs are taken over in SAP ERP.
„Previously the transfer of this data was a time-consuming feat, with ORBIS PCC this task is now completed with only a few clicks of the mouse“, Uwe Oltmanns reports.
Uwe Oltmanns, System Analyst & Controller Corporate Purchasing, CLAAS KGaA mbH
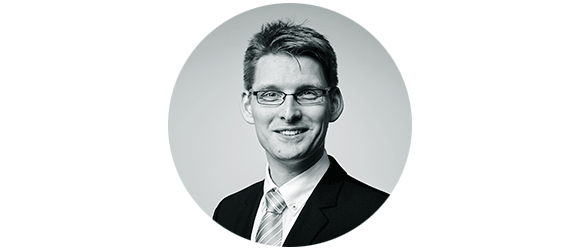
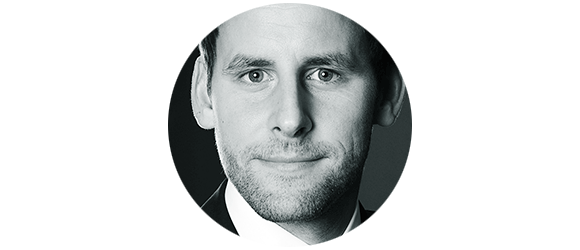
Jan Kirberich, Lead Engineer Simultaneous Product Costing, CLAAS Group
Also, the effort for adjusting the calculation during the year, which becomes necessary when the construction model needs to be technically modified, is very low. For new materials or work materials for which no material number has yet been allocated in the SAP software, “Material Dummy” placeholders are first created in ORBIS PCC, complete with a price and a short description. As soon as the actual material price is stored in SAP ERP, the correct value is entered in the Dummies.
Flexible implementation of extra requirements
Because each calculation version created with ORBIS PCC is stored in SAP ERP, any changes or deviations can be retraced with the calculation comparison, right down to the individual item level. This feature was originally specifically developed for CLAAS, however, in future it will be integrated as a standard feature in the add-on, allowing all customers to benefit from this.
Introduction in just under six months
In addition to the full integration into SAP ERP and its tremendous flexibility, the attractive price of the license model was a decisive factor for choosing ORBIS Product Cost Calculator. Thanks to the process and consultancy expertise and personal commitment of the ORBIS experts as well as the cooperation of all involved, which was marked by partnership, the implementation could be completed at the German sites in just under six months, and this according to the budget. However, CLAAS is not fully satisfied yet. The next step is the roll out of ORBIS PCC in the global manufacturing companies and additional extensions are also in planning.